Don't Make Costly Jacking Mistakes
It's definitely a job for the professionals, but if you decide to take on a heavy jacking operation yourself, there are some basic procedures you need to follow to keep everyone safe
We were recently contacted by a new customer to provide emergency assistance at a local hospital, where they had attempted to lower a 24-tonne generator using hydraulic toe-jacks (the generator had been landed onto timber by a mobile crane and subsequently needed to have the timber removed to lower the machine to final position). Unfortunately, they failed and managed to leave the generator in an unstable condition.
Luckily no-one was injured on this occasion, but we do know of other instances where people have been hurt and even fatalities have occurred due to inexperienced jacking operators losing a load.
With that in mind, I thought it would be worth running through some of the basic principles required to carry out a manual jacking operation safely.
Novatec Engineering Ltd would always recommend the use of qualified and experienced personnel to carry out any industrial lifting operation and are happy to help whenever required - just get in touch using the details at the bottom of the page.
For anyone intending to go it alone, please read on...
When raising a heavy machine using manual hydraulic jacks, the most important factors to consider are:
1. Choose the right jack:
Select the appropriate type and capacity of jack for the load you need to lift.
When deciding on rating capacity, don't just select a jack capacity that matches the weight of the machine being lifted. You probably won't be using a single jack anyway (particularly if you're lifting the whole machine clear of the floor). We generally use manual hydraulic jacks in pairs, to raise each end of a machine in turn and would normally ensure each jack is rated to at least half of the total machine weight. This way, if one jack should fail or encounter a problem, the second jack is not overloaded.
This should always be considered in the written lift plan or method statement in place for the operation - as a side note, always make sure an appropriate lift plan is prepared and documented by a competent person before allowing any lift to take place on your site.
2. Ensure that the jack is in good working condition.
Follow these steps to ensure the jack is in good working condition:
- Inspect the jack for any signs of damage, such as cracks, dents, or leaks. If any damage is found, the jack should not be used and should be repaired or replaced.
- Check the hydraulic fluid level in the jack. The fluid should be at the correct level as indicated in the manufacturer's instructions. Top up the fluid if necessary.
- Ensure that the release valve operates properly and is not stuck or damaged. Test the valve by turning the handle to release the hydraulic pressure and verify that it returns to its closed position.
- Check that the lifting arm and saddle are straight and not bent or damaged. The saddle should be able to swivel freely and lock securely in place.
- Test the jack by lifting a load that is within its weight capacity. Observe the lifting process to ensure that the jack operates smoothly and the load remains stable.
- After lifting the load, lower it slowly and evenly, ensuring that the jack operates smoothly.
- Ensure the jack is stored in a clean, dry location, away from any heat sources or corrosive substances.
Performing regular checks of your jacks, aside from being a statutory requirement, is important to ensure their safe operation and prevent accidents. Always refer to the manufacturer's instructions for specific maintenance and inspection procedures.
3. Stability: Ensure that the jacks are placed on a stable and level surface to prevent tipping or rolling.
Place the jack on a stable, level surface and ensure that the load is properly positioned on the jack. The load should be centered over the jack and balanced to prevent tipping.
Always use a suitable spreader plate or pad below the jack base. This will help spread the load and help improve stability.
Several factors can cause jack instability during a lift, including:
- Uneven weight distribution: If the weight of the load is not evenly distributed on the jack, it can cause the jack to tip or become unstable.
- Exceeding weight capacity: If the weight of the load exceeds the weight capacity of the jack, it can cause the jack to fail or tip over.
- Uneven surface: If the jack is placed on an uneven or sloped surface, it can cause the jack to tip or become unstable.
- Misalignment: If the jack is not properly aligned with the load or if the load is not centered on the jack, it can cause instability during the lift.
- Overextension: If the jack is extended beyond its maximum height or reach, it can cause instability or failure.
To prevent jack instability during a lift, it is important to follow proper lifting procedures and use jacks that are appropriate for the weight and size of the load. Always inspect the jack before use, and ensure that it is on a stable, level surface. Position the jack directly under the center of gravity of the load, and lift the load slowly and evenly to prevent tipping or imbalance.
4. Lift Evenly:
Use the jack handle to lift the load slowly and evenly, keeping the load centered over the jack. Avoid overextending the jack beyond its recommended height.
When lifting with multiple manual jacks, ensure the lift phase is coordinated between the operators, so they lift or lower at the same time.
Ensure suitable packing timber, chocks, blocks, or other devices are used to secure the load and prevent it from shifting during the jacking operation.
When jacking in stages, never over-lift at one end (risking slipping or overturning of the load) and always follow the jacking operation with appropriate physical blocks, as a safeguard against jack failure.
5. Use safety equipment
Wear appropriate personal protective equipment, such as riggers gloves and steel-toed boots. In addition, never place hands and feet (or any other body parts) underneath a load raised on hydraulic jacks alone - as above, always use appropriate blocks to follow the load up.
Summary
Whilst a seemingly straight-forward operation, jacking a heavy machine can be a complex task, requiring experience and care to perform safely.
If taking it on yourself, ensure you follow the basic steps outlined above and that your personnel have the appropriate skills and training to carry out the work safely.
If you're in any doubt, consult a professional machinery handling company, like Novatec Engineering.
Don’t risk your machinery or the safety of your personnel - Trust Novatec’s experience and expertise to get the job done properly
Over the years, our team has handled everything from a single machine to complete factories for a variety of different clients and in all industries from food production to waste recycling (and everything in between).
Regardless of the size of the project, our team follows the same strict procedures to ensure your machinery is handled safely and efficiently and is back in operation to suit your requirements.
Trust us to look after your machinery needs in every aspect, from planning and management to decommissioning, movement, re-installation and commissioning. Get in touch with our friendly team and we’ll be only too happy to advise on the next steps for your project.
Call 01634 757455 or email the team at office@novatec-engineering.co.uk
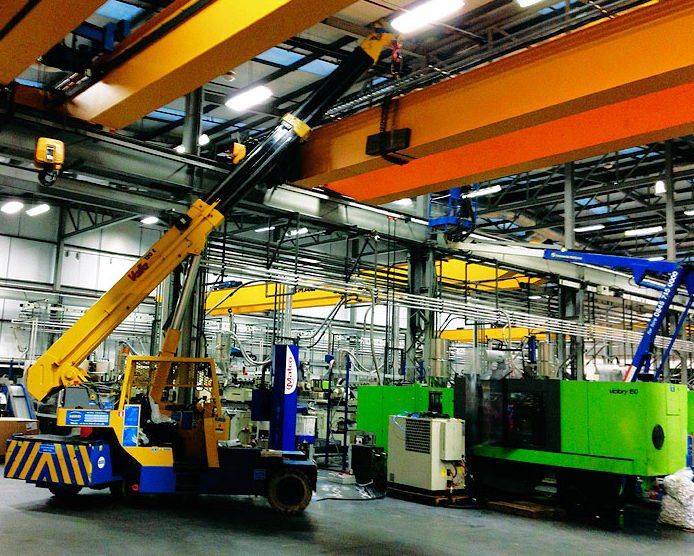
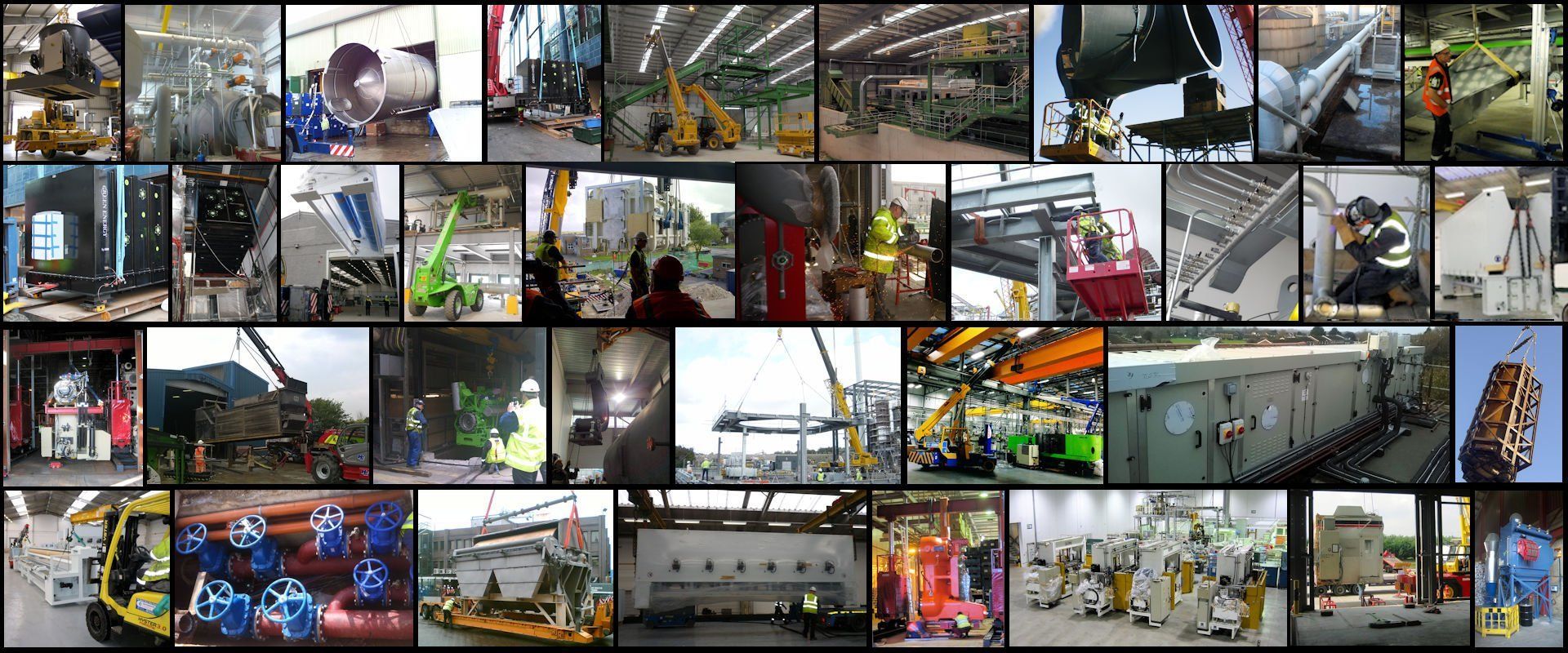